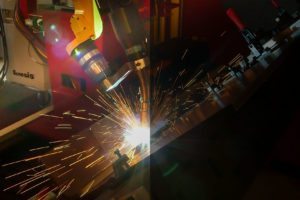
Robotic welding is widely recognized for its efficiency in large-scale, repetitive tasks. These operations typically involve minimal adjustments to programming or tooling, ensuring consistent uptime. However, this doesn't mean robotic welding isn't suitable for smaller-scale production runs. While the initial setup might seem daunting, modern advancements in automation make it increasingly feasible for even small businesses to harness the benefits of robotics.
The decision to implement robotic welding ultimately depends on whether it can deliver a return on investment (ROI). For smaller companies, determining this can be tricky, as the costs associated with purchasing and integrating robotic systems must be weighed against potential gains. Despite these challenges, technological progress has made robotic welding accessible to businesses of all sizes.
Why Consider Robotic Welding?
If you're unsure about adopting robotic welding, it's worth understanding the motivations driving many small enterprises toward automation. One primary reason is the desire to stay competitive in a market dominated by larger firms. Established companies often have the financial flexibility to adopt advanced technologies like robotic welding early on, creating an edge over smaller competitors. To remain relevant, smaller businesses may need to follow suit at some point.
Another pressing concern is the ongoing shortage of skilled welders in the U.S., which is expected to worsen unless addressed. According to the Department of Labor, the industry needs to hire thousands of new welders annually just to meet current demands. By automating certain aspects of welding, companies can mitigate staffing issues while maintaining productivity.
Key Factors for Achieving ROI in Small Batch Welding
While every business scenario is unique, there are specific criteria that can increase the likelihood of achieving ROI through robotic welding in small-batch settings. Flexibility is key—your robotic system should accommodate diverse part types without requiring extensive reprogramming each time. A versatile workspace with multiple axes allows for seamless transitions between jobs.
Efficient offline programming tools are equally critical. Training existing employees to manage robotic systems leverages their existing knowledge of welding techniques. Moreover, collaborating with experienced system integrators ensures your team gets up to speed quickly upon installation, maximizing output almost immediately.
Other considerations include selecting durable components designed for longevity, ensuring easy maintenance, and optimizing workflow integration. These elements contribute significantly to long-term success and profitability.
Though it requires careful planning and execution, realizing ROI from robotic welding in small batch environments is entirely achievable. Partnering with knowledgeable integrators familiar with similar applications can provide valuable insights tailored specifically to your needs.
For further guidance, explore real-world examples of robotic welding implementations across various industries. Such case studies can offer practical inspiration and demonstrate how others successfully navigated comparable scenarios.