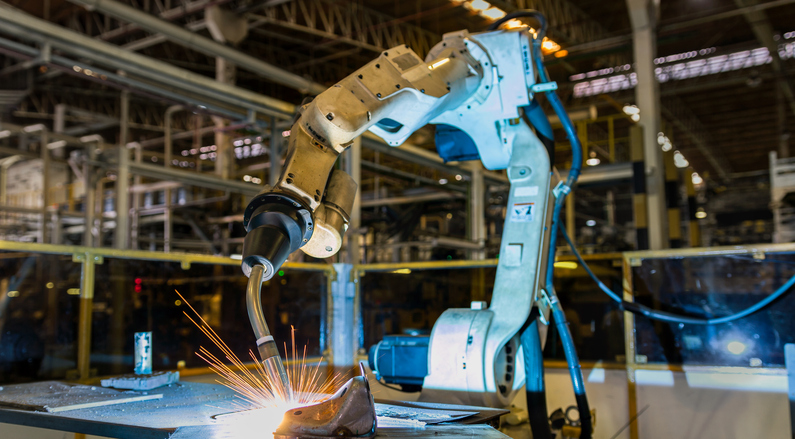
When it comes to industrial robotics, the end-effector—or end-of-arm tooling (EOAT)—is often overlooked but plays a pivotal role in determining the success of a robotic system. While the robot arm itself is designed to provide motion and flexibility, it’s the end-effector that ultimately interacts with the workpiece, transforming the robot into a specialized tool for specific tasks.
Manufacturers typically do not include the EOAT in their original design; instead, it is added later by an integrator to tailor the robot to a particular application. This customization is what makes industrial robots so versatile and efficient. However, selecting the wrong end-effector can lead to significant inefficiencies, including slower cycle times, increased downtime, and even damage to the robot itself.
How to Choose the Best End-Effector
Selecting the right end-effector is a meticulous process that requires careful consideration of several factors. This is where the expertise of a seasoned robotic systems integrator becomes invaluable. Typically, the selection process begins with a thorough analysis of the application requirements, including payload capacity, operating speed, workspace limitations, and environmental conditions.
For instance, in material handling applications, the choice might hinge on whether the object to be handled is lightweight and delicate, requiring a vacuum gripper, or bulky and robust, necessitating a mechanical gripper. Other considerations include the part's geometry, surface texture, and fragility, all of which influence the type of EOAT required. Additionally, in environments where space is limited, compact EOAT designs become essential.
In some cases, quick-change tools are employed to allow the robot to switch between multiple end-effectors during a single operation. This flexibility ensures that the robot can adapt to varying tasks without halting production, maximizing efficiency and output.
Why the Right End-Effector Matters
Using the wrong end-effector can have cascading effects on a robotic system's performance. A poorly matched EOAT can result in frequent stoppages due to dropped parts, misaligned components, or even mechanical failure. These issues not only reduce productivity but also increase maintenance costs and extend the time needed to achieve a return on investment (ROI).
On the other hand, the right end-effector enhances the robot's capabilities, enabling it to execute tasks with precision and speed. Whether it's assembling parts, welding seams, or packaging products, the end-effector directly impacts how efficiently the robot completes its job. When paired with the appropriate EOAT, the robot can operate at its full potential, delivering consistent results and reducing operational costs.
Moreover, the right end-effector can open doors to new opportunities. For example, advanced end-effectors equipped with sensors or vision systems can enable robots to perform complex tasks like quality inspection or adaptive machining. Such innovations contribute to the robot's versatility and long-term value within a manufacturing process.
Ultimately, the success of a robotic system hinges on the compatibility between the robot arm and its end-effector. A well-chosen EOAT ensures that the robot operates smoothly, minimizes downtime, and maximizes profitability. Working with a knowledgeable integrator who understands both your industry's unique challenges and the nuances of robotic technology is key to achieving these goals.
To explore how Genesis Systems Group can help optimize your robotic solutions, visit our website and discover our comprehensive range of robotic tooling services. From concept to implementation, we’re committed to helping you unlock the full potential of your robotic investments.
Posted in Robotic Applications