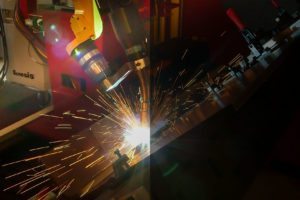
Robotic welding is often associated with high-volume, repetitive tasks, where the system can run continuously without frequent adjustments. However, this doesn't mean it's unsuitable for smaller-scale operations. With recent advancements in automation technology, even small businesses can find ways to integrate robotic welding systems and see a positive return on investment (ROI).
While the upfront cost of robotic welding systems might seem daunting, the long-term benefits can outweigh the initial expense. For small businesses, achieving ROI means balancing the costs of the system against its productivity gains. These gains come from increased speed, precision, and consistency in welding operations, which translate into reduced labor costs and higher output quality.
Why Consider Robotic Welding for Your Business?
Even if you're unsure about the potential ROI, there are compelling reasons to explore robotic welding solutions. One of the primary motivations is to level the playing field with larger competitors. Big companies typically have greater financial resources to invest in advanced technologies like robotics, giving them an edge in terms of efficiency and capacity. By adopting similar technologies, smaller firms can maintain competitiveness and stay relevant in the market.
Another pressing reason is the current shortage of skilled welders. The U.S. Department of Labor predicts a significant demand for new welders over the next decade. Automating welding processes with robots can alleviate the pressure caused by this shortage, ensuring consistent production levels without relying heavily on human operators.
Key Requirements for Achieving ROI in Small Batch Production
Not all welding applications are created equal, so achieving ROI in small batch production requires specific considerations. Flexibility is key—if your production involves multiple part types, your robotic system must be adaptable enough to handle each one efficiently. A flexible work envelope with multiple axes allows the robot to adjust easily between tasks, maximizing productivity.
Efficient offline programming is another critical factor. Training existing welders to operate the robots can leverage their practical knowledge while reducing training time. Moreover, partnering with a skilled system integrator who offers robust offline programming tools can significantly expedite the setup process, allowing the robots to begin contributing to production almost immediately upon arrival.
Other factors, such as ease of maintenance, integration with existing equipment, and customization options, also play crucial roles in determining whether a robotic welding solution will deliver the desired ROI. It's essential to evaluate these aspects carefully when selecting a vendor or integrator.
While it may require careful planning and execution, realizing ROI through robotic welding in small batch environments is entirely feasible. The success hinges largely on identifying the right combination of features tailored to your unique needs and choosing an experienced integrator familiar with similar applications.
For further insights into how robotic welding can enhance productivity across diverse industries, take a look at our collection of real-world case studies showcasing successful implementations. Each example highlights specific challenges overcome and outcomes achieved, providing valuable guidance for businesses considering this path.