In every manual for thread cutting, there's always a strong recommendation to use cooling lubricants for screw taps. This advice should never be overlooked! The process of cutting threads generates friction, which leads to increased heat, tool wear, and poor surface finish on the threads. Without proper cooling lubricants, both the tap and the component being machined are at risk of damage.
When it comes to tap lubrication, there is a wide range of products available, each with unique properties tailored for different applications. These can vary from the consistency of the lubricant to the inclusion of special additives that provide benefits such as **corrosion protection** or **improved lubrication performance**. With so many options on the market, it can be challenging to choose the right one. We’ll break down the differences and guide you on what to look for when selecting cooling lubricants for taps.
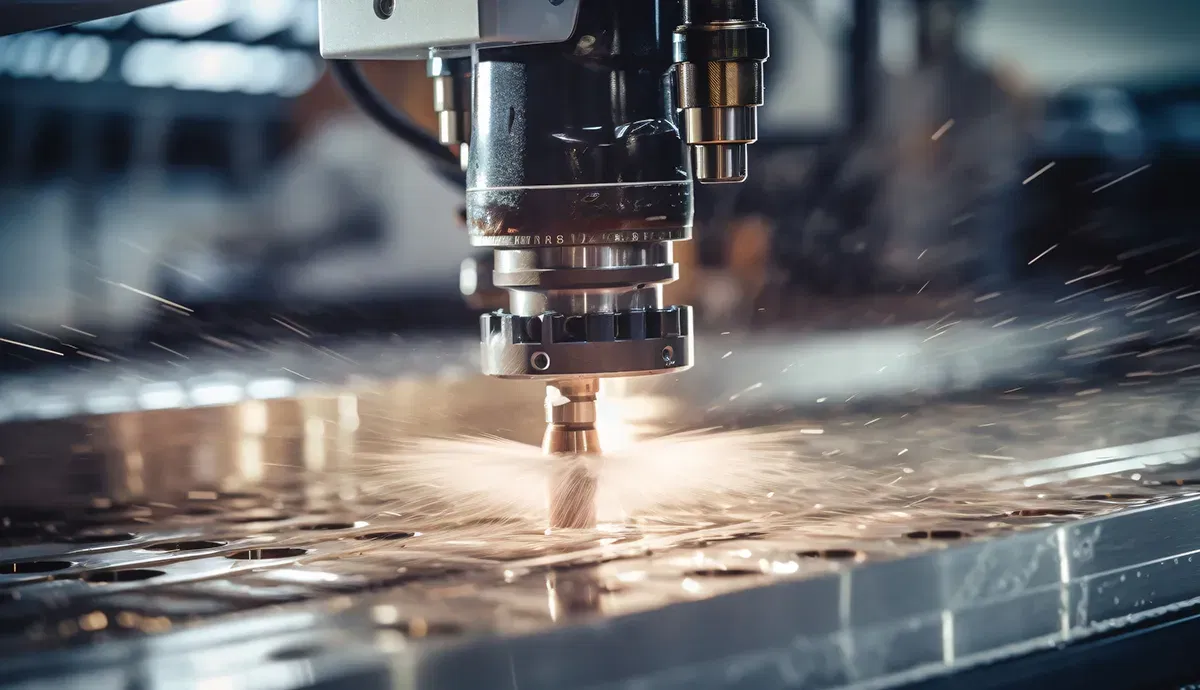
Cooling lubricants for screw taps must perform several key functions. As their name suggests, they are designed to cool and lubricate. However, these two roles are not always equally important. Depending on the machining process, one function may take precedence over the other. For example, the need for cooling is more significant at higher cutting speeds, while lubrication becomes more critical during slower operations. Therefore, **lubrication is often given greater emphasis** in cooling lubricants for screw taps.
In addition to cooling and lubricating, these lubricants also help in chip removal. They ensure that the **material being cut is efficiently carried away**, which is especially important in industrial settings where large volumes of coolant are used continuously.
The main roles of cooling lubricants for screw taps include:
- Cooling effect
- Lubricating effect
- Chip removal
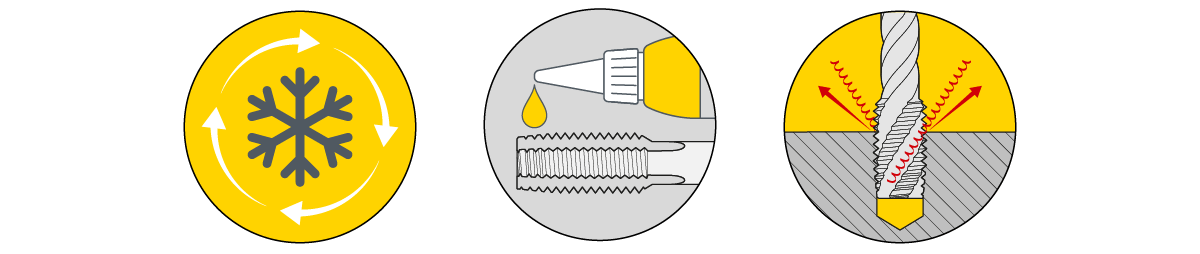
Cooling lubricants are standardized according to **DIN 51385**, which categorizes them into water-miscible and non-water-miscible types. Each type has its own advantages and is suitable for different applications. Additives such as **EP (extreme pressure) additives** or **high-pressure additives** can significantly improve the performance of these lubricants.
**Non-water-miscible coolants** typically consist of mineral oils with various additives. These coolants form a durable oil film on the metal surface, providing excellent lubrication and resistance to pressure. Common additives include corrosion inhibitors, foam suppressants, and anti-fog agents.
**Water-miscible coolants**, on the other hand, are mixed with water before use. Since water is an efficient heat conductor, these lubricants are particularly effective at dissipating heat. They often contain emulsifiers, antioxidants, and corrosion inhibitors, along with EP additives.
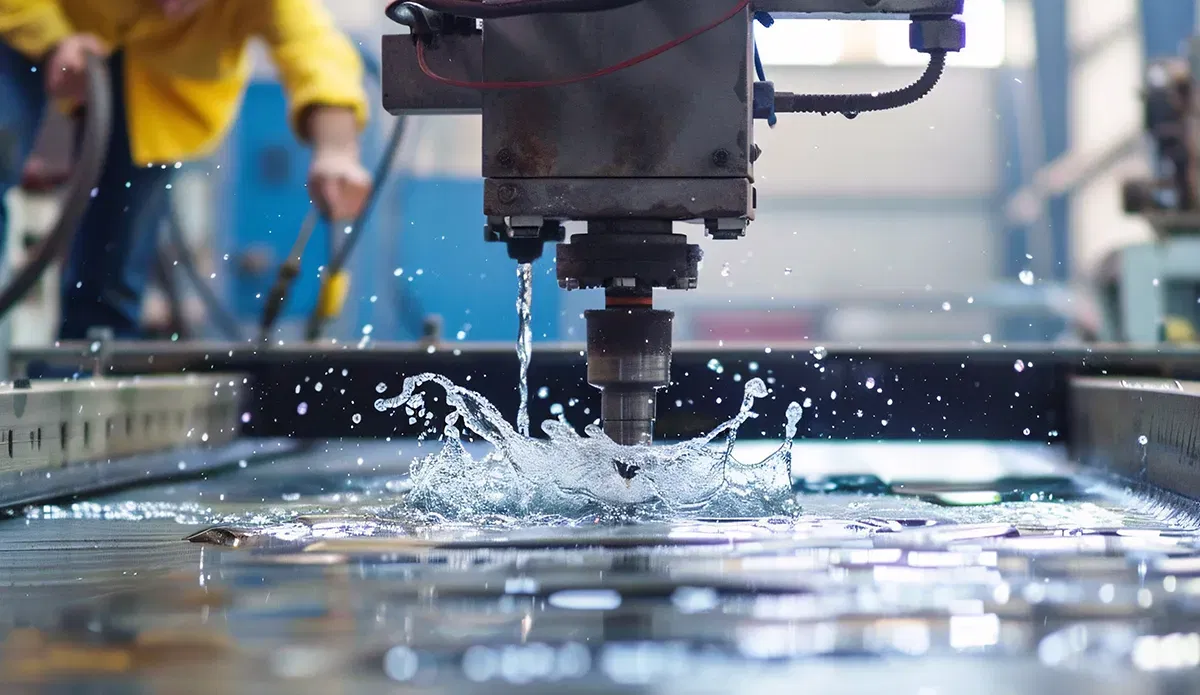
The choice of cooling lubricant depends largely on the material being machined. When cutting threads into **steel**, water-miscible coolants are commonly used and should be applied evenly for optimal results. For **hard-to-machine alloys** like INCONEL, non-water-miscible coolants may be preferred. These are usually more fluid and require larger quantities to cover the work area effectively.
Working with **magnesium** requires extra caution. Using water-miscible coolants can lead to the formation of **magnesium hydroxide and hydrogen**, which could create explosive mixtures. To reduce this risk, a coolant with a high pH level is recommended.
Similarly, when machining **titanium or its alloys**, it’s important to avoid coolants containing **chlorine**, as this can cause **stress-corrosion cracking**.
In industrial environments, the supply of cooling lubricants for threading tools must be consistent and even. A small interruption in the lubrication film can have serious consequences. Coolants can either be **directly supplied through the tool** or **sprayed externally** from nozzles.
For hobbyists or those working in a garage, the process is simpler. Just manually apply your chosen cooling lubricant to the tap and reapply as needed. This ensures a smooth and efficient threading process.
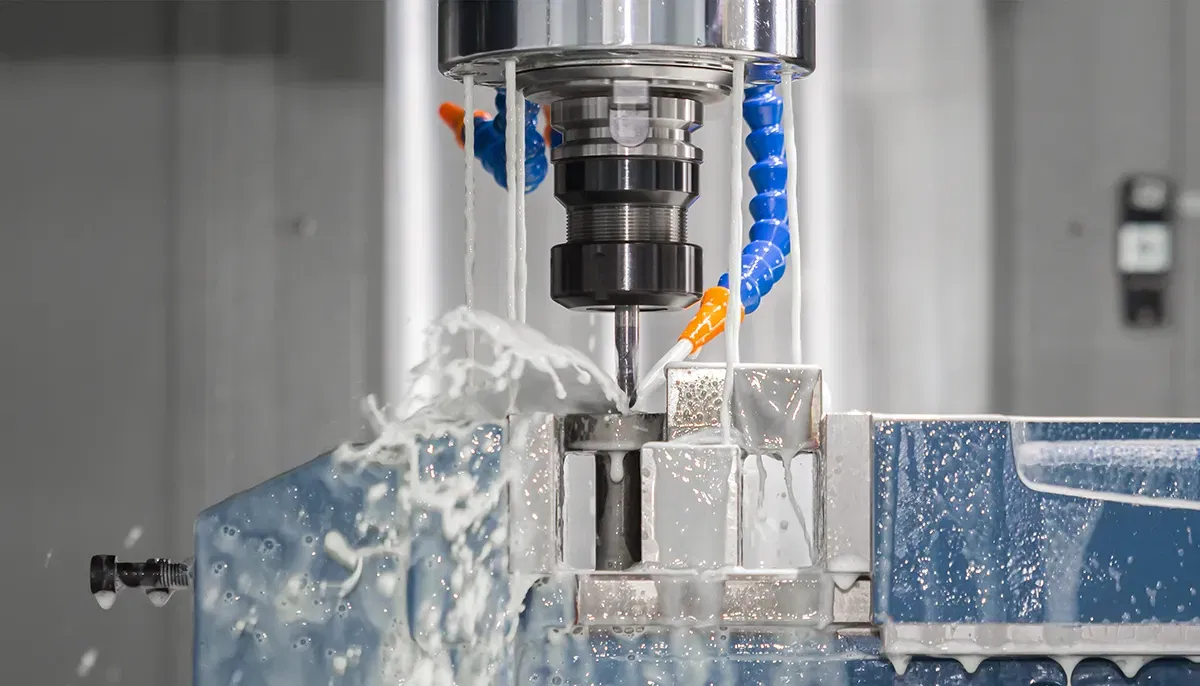
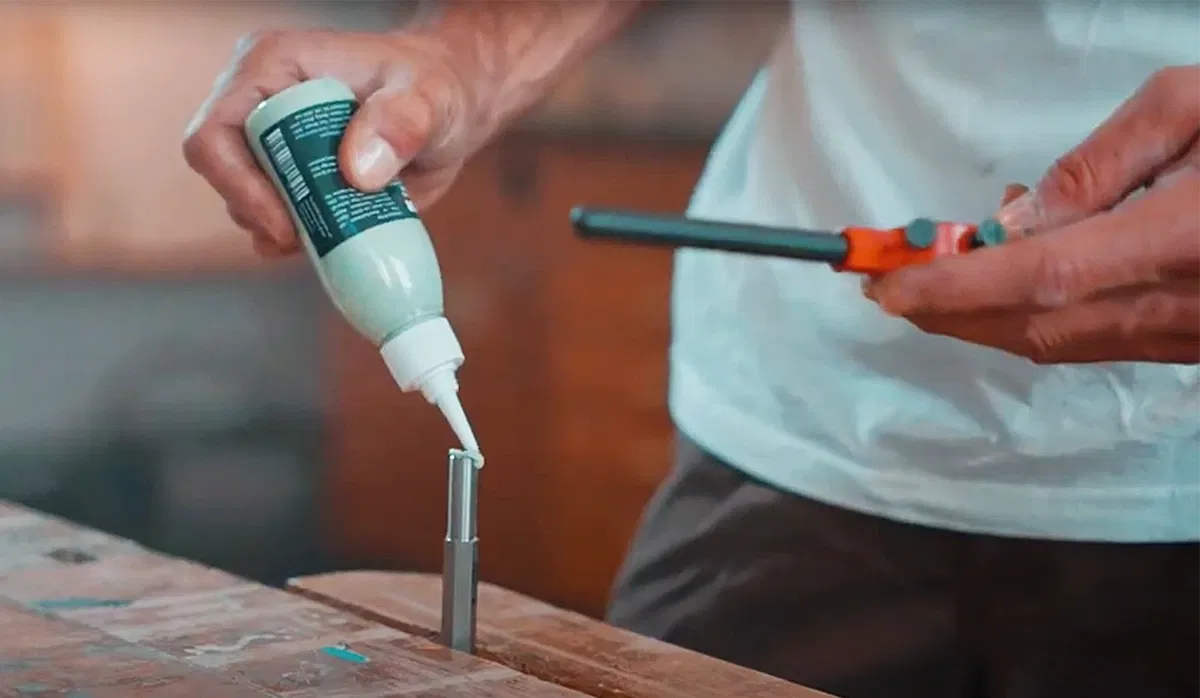
Choosing the right cooling lubricant for screw taps is a careful process. Factors such as cutting conditions, the type of tap, and the material being worked on all play a role. While these considerations are most relevant in **industrial production**, where efficiency and cost-effectiveness are crucial, they still matter for long-term use.
For occasional threading in a workshop or home setting, **universal products** often work well. Just make sure the coolant is specifically designed for screw taps and comes from a trusted source. That way, your project will go smoothly, and you won’t have to worry about rare but dangerous situations like hydrogen explosions.
If you're looking for a reliable cooling lubricant for screw taps, consider checking out the **cutting paste** available in the online shop of **BAER**, a leading manufacturer of screw taps. It’s suitable for a variety of materials and applications, easy to use, and free from **petroleum, chlorine, and sulfur**. If you want more information, our customer service team is always here to help!
Drying Machine
Pharmaceutical Bolling Granulating Dryer,Fluid Bed Dryer,Vibration Fluid Bed Dryer
Jiang Yin Jun Lang Machinery Co.,Ltd , https://www.fluidbeddry.com